The sampling technique is known as AQL, or “Acceptance Quality Limit,” is crucial for quality control. It is described in ISO 2859-1 as “The worst tolerable quality level” over the course of numerous inspections.
When an inspector visits your manufacturer to evaluate the quality of the product, they use AQL sampling to address two key issues:
- How many units in a particular shipment should I inspect?
- How many flawed products are permitted before the inspection is deemed to have failed?
Understanding AQL is essential when importing consumer goods so that you can cooperate with your inspectors. If you don’t fully comprehend the methodology, you run the risk of interpreting your inspection findings incorrectly, which can result in quality catastrophes.
Here, we give a brief explanation of the AQL chart’s operation. You’ll discover how to use the AQL tables to respond to the previous two questions.
The Chart of Acceptance Quality Limits (AQL)
The two tables that make up the AQL chart are shown below. Additionally, the ANSI/ASQ Z1.4 tables are another name for them. Additionally, you can use them in order to calculate your sample size and the maximum number of defects per lot.
These tables were developed over time with the help of statisticians like Harold F. Dodge and others. At the Pentagon during World War II, Dodge created quality control guidelines for testing US military hardware.
Today, importers use AQL to inspect consumer goods, including clothing, furniture, and appliances. To clarify how to use the tables, we’ll use an example involving reusable plastic cups in the following section.
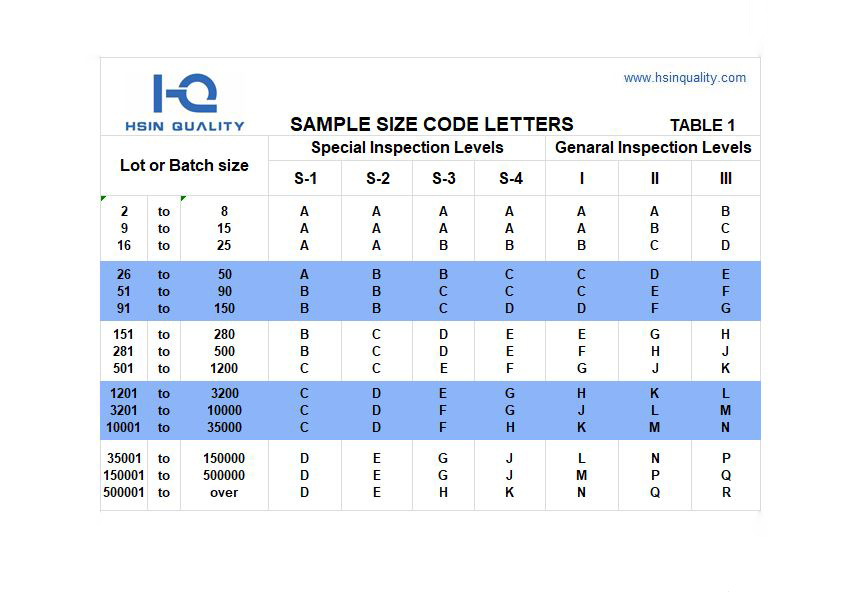
Instructions for Using the AQL Tables (An Example: Examining Plastic Cups)
Consider that you’ve given your factory an order for 1,500 reusable plastic cups. A third-party product inspection business (like Insight) has been hired to visit your factory before the order is shipped. The number of random samples they should take will be determined using Table 1.
Table 1 shows examples of size code letters.
Your purchase order contains 1,500 cups, so you can choose the appropriate range by looking at the “Lot or batch size” column on Table 1’s left side. The correct lot size in this instance is ‘1201 to 3200,’ which is highlighted in red.
The inspector will examine a certain number of products, depending on the level of inspection you select. You can see that I’ve underlined “General Inspection Level II” in red. Generally speaking, General II can be used for most consumer goods. Later, we’ll go into greater detail about the other levels.
For the time being, seek out the point where your ‘Lot or batch size’ row and the ‘General II’ inspection level column intersect. You’ll notice that we’ve circled in red the “Sample size code letter,” which is “K.” This code letter will be used in the following table.
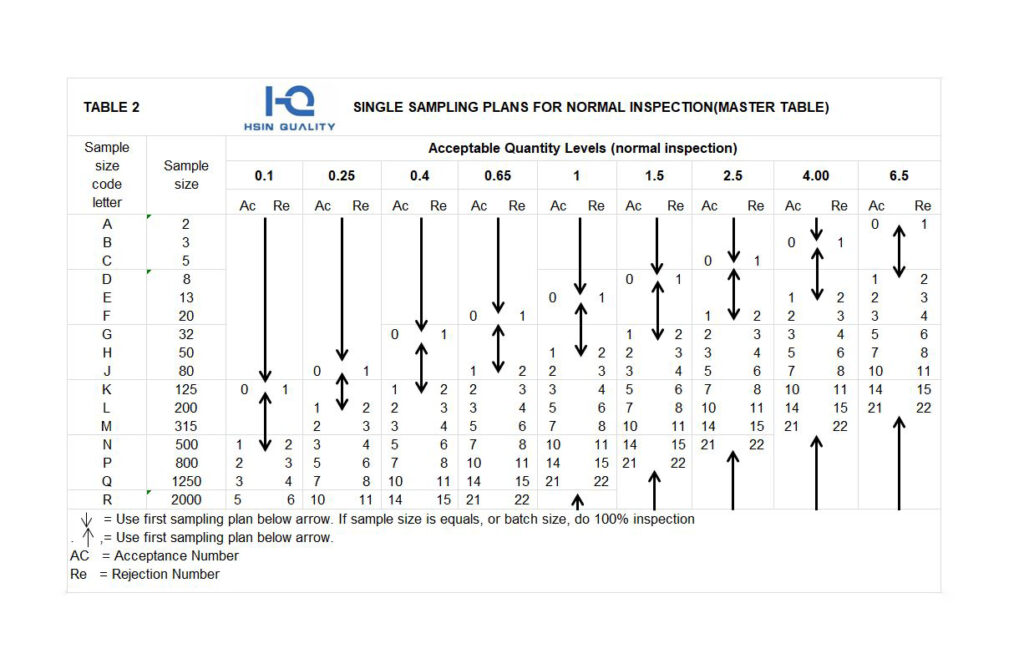
Table 2 displays Single Sampling Plans for a Normal Inspection.
We will choose “K” from the list on the left of Table 2 because we now know your “Sample size code letter” from Table 1 is “K.” We can see that the inspector will need to examine 125 randomly chosen cups from your shipment of 1,500 cups in the column above, under “Sample size.”
You’ll notice a number of columns representing various Acceptable Quality Levels to the right of “Sample size.” Standard AQL levels for the majority of common consumer goods are 2.5% for major defects, 4.0% for minor defects, and 0% for critical defects. That is why “2.5” and “4.0” above have been underlined.
By applying this standard, we can determine that your inspector will approve up to:
- 7 major defects, and
- 10 minor defects.
A shipment will not pass inspection if it has 8 major defects, 11 minor defects, or 1 critical defect. As a result, your inspector has the criteria necessary to decide whether to pass or fail. Read our article on AQL defect classification if you’re not sure what major, minor, and critical
The AQL Chart: Three Crucial Concepts to Know
We have presumptions in the example we gave above. This was a first in that Table 1 would use General Inspection Level II. The second was that major defects would be measured at 2.5% AQL and minor defects at 4.0% AQL. We will talk about some
What are the General Inspection Levels? (Table 1)
There are three General Inspection Levels — I, II, and III. How many units to inspect is primarily determined by the level you select. In our example, we chose Level II because it’s the most typical option for goods marketed to general consumers. Your sample size ended up being 125 cups as a result.
Instead, if you had selected Level I, the inspector would have only examined 50 cups. On the other hand, if you had selected Level III, they would have looked at 200 cups.
Why might you choose Level I or III?
Since the inspection takes less time, there are times when inspecting fewer units (Level I) can lower costs. The drawback is that you might be less confident in the outcome. If you have a strong relationship and level of trust with your supplier, only then should you perform a Level I inspection.
On the other hand, you might decide to inspect additional units if you are working with a new factory or have had a string of recent failures (Level III). An inspection with a larger sample size will take longer and cost more to complete, but the results will be more reliable.
Check out our article on the General Inspection Levels for more details.
Which Special Inspection Levels are there? (Table 1)
There are four different levels of special inspection: S-1, S-2, S-3, and S-4. You will get a smaller sample size using the Special levels than you will with any of the General levels. In contrast to the 125 cups from General Level II, the inspector will only check 5 cups if you use Special Level S-1 on an order of 1,500 units.
What uses of the special inspection levels do you have in mind?
The Special Inspection Levels do not generally apply to the entire inspection. The tests on your quality inspection checklist that they do apply to are only certain kinds of tests. For instance, you could use General II to evaluate craftsmanship by looking for blemishes, smudges, or cracks in the product, and you could use Special S-1 to examine the outer carton’s dimensions.
You can typically employ the Special Inspection Levels when:
- Testing harms the quality of your product,
- Testing is extremely complex, time-consuming, or both.
- There are some defects that don’t need to be fixed right away, so act quickly.
What Are the Different AQL Levels, Like 1.0, 2.5, 4.0, etc.? (Table 2)
The AQL percentage you have selected for your product is represented by these various levels. Remember that over the course of numerous inspections, they represent the maximum percentage of flaws you are willing to overlook.
The typical AQL levels for common consumer goods are as follows:
- Major defects at 2.5 percent
- 4% for minor flaws
- 0% for serious flaws
Major flaws render your product unsellable or cause customer returns, whereas minor flaws only involve minor deviations from your specifications. “Critical” flaws are those that could endanger the consumer’s safety.
A Few Frequently Asked AQL Questions
One or more of the following queries may be on your mind.
① Why Should I Use AQL Instead of Inspecting 100% of My Products?
You might think, “I’d have 100% certainty with a 100% inspection, so it must be the better option.” And if you are purchasing low volumes, this is reasonable. However, as your order quantities increase, complete inspections become less practical. The inspection will take longer to complete and cost more money.
The AQL statistical model has been successfully applied for many years. It’s widely used in the quality control industry because it’s effective, which is why. It’s crucial to keep in mind that performing an AQL inspection won’t ensure a defect-free inspection because that isn’t what it’s there for. For more information
② What Takes Place When I Touch an Arrow in Table 2?
Use the sampling plan above the arrow if it points up; use the plan below the arrow if it points down. For illustration, suppose you ordered 90 pairs of wireless headphones and chose General II and a 2.5% tolerance for major flaws.
You move to the lower sampling plan because the code letter E places you on a down arrow. 20 sets will be inspected, with the lot being accepted if there is only one defect and rejected if there are two.
③ Why Do the “Accept” Numbers Differ from the Percentage I Selected?
Consider the scenario where you have ordered 3,200 sets of tables and chairs. Your code letter is K and you have chosen General II and 2.5% for major defects.
If you had 125 samples, you would accept 7 defects but reject the entire lot if there were 8. Why is it that there are 7 defects or 5.6% of the 125 units you are inspecting?
You should keep in mind that AQL is a probabilistic statistical tool. Not the percentage of defects in the sample size, the 2.5% represents the anticipated long-term average defect rate over many lots.
④ The samples are chosen from how many cartons?
Consider that you placed an order for 1,000 units of your product and decided to examine an 80-unit sample size. You are unsure of how many cartons to take samples from because your products are shipped in cartons that contain 10 units each.
The inspector always calculates this by taking the square root of the total number of cartons plus one. They choose 11 of the 100 cartons and take the samples from those.
⑤ Does AQL Promise There Will Be No Defects in My Shipment?
The quality levels you think are best for your product are used to determine the AQL. In essence, it is not intended to guarantee a defect-free product. Generally speaking, outside of high-risk industries like aerospace or pharmaceuticals, expecting zero defects is unreasonable.
But AQL is adaptable and lets you set higher benchmarks for your brand. Making your standards more stringent, you might decide to use an AQL level of 1.0% for major defects rather than the industry-standard 2.5%. A high-end brand might benefit from this kind of adjustment.