
Management System Training
All-Inclusive – Inspection Service All Over China
Compliance with safety and brand standards, quality control, and other factors depend on effective inspection management. Maintaining consistency in maintenance, making sure problems are discovered and resolved more quickly, and ensuring that routine inspection procedures are followed are all made possible by managing the process and adhering to it.
Many operations have historically used paper tracking techniques, such as clipboard inspection checklists and protocol binders, to keep track of inspections. Although paper tracking is effective, it has issues with accessibility and handoffs.
When attempting to maintain open communication between teams, analog inspection tracking tools can only be used to a certain extent. Paper documents can be lost more easily, but also different handwriting styles and filing systems can result in misunderstandings or even missing information. Things getting overlooked here and there might not seem like a big deal, but when it comes to inspections, even the smallest bit of missing information can mean the difference between putting out a fire and completely preventing it.
This is where the overall inspection tracking process can greatly benefit from the use of contemporary inspection management software. Information and documentation are easier to access, more standardized, and more understandable when they are created using the proper digital solution.
Exactly why is proper inspection management important?
Regular inspections raise the general level of safety, quality, and consistency of sites, resources, and products in almost every sector.
Regular inspections of the amenities and guestrooms, for instance, at a hotel, guarantee that the rooms and furnishings are consistently maintained in good working order for visitors. Without these routine checks to help with planning for maintenance needs and making last-minute fixes where necessary, guests risk arriving for their stay and discovering the HVAC unit in a room is broken or the television isn’t working properly. These issues may seem minor, but if they cause your clients and customers—in this case, guests—uncomfortable situations, it could negatively affect both your reputation and your bottom line. And it’s likely that there will be more than one instance of improper process issues. For instance, in a hotel without routine inspections, breakdowns and safety concerns will eventually start to affect visitors.
Poor safety inspections in the manufacturing and construction industries can result in workplace accidents, costly medical expenses, and legal action. The risk of non-compliance increases and threatens profitability in the absence of routine inspections.
Inspections give you and your team a regular opportunity to review important safety, compliance, and quality concerns. It is essential to have standard operating procedures for inspection processes and to manage those processes properly if you want to keep your properties, assets, and services operating smoothly and guarantee the caliber of your clientele’s offerings.
Five Qualities of an Effective Inspection Management
Modern inspection management software makes it possible to use digital tools for tracking, managing, and even concluding inspections. With the right software, you can perform inspections while on the go, communicate inspection protocols with your team, and adapt checklists to your specific workflow and needs. The following traits of efficient inspection management software are also present:
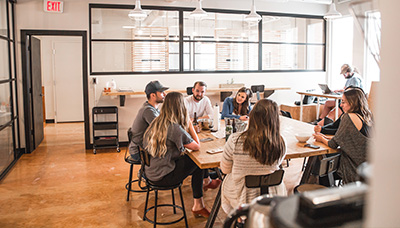
1. An already-built inspection template library
Although many contemporary software programs come with inspection capabilities, the best inspection software comes with pre-built inspection templates right out of the box. This enables you and your team to begin managing your inspections right away while you decide on the best digital tools for your team and create templates that are specific to your individual workflows. The templates still provide a strong foundation upon which modifications and additions can be made even if they are not exactly in line with your process.
2. Attachments for photos and notes on inspection items
The flexibility to add images and notes to specific inspection items is a feature of good inspection software. This enables the team to communicate clearly and supply the information required for work orders or maintenance requirements, for instance, if something is broken in a hotel room, your team can attach a picture to show what is wrong and precisely what is required to fix it. Overall clarity is improved, and team members can communicate less back and forth as a result, which speeds up problem-solving.
In construction, a key use case of inspections is creating punch lists that identify deviations between plans and actual work to make necessary corrections before closing out the job. Strong inspection tools can facilitate and expedite this typically drawn-out process.
3. Flexible Forms for Every Inspection
Multiple input formats will also be supported by the ideal inspection software. This allows your team to easily include required or necessary information while also allowing you to check off inspection items in the manner that works best for your process. The software allows for inspection and checklist items to have required text fields, be marked simply as pass/fail, include number inputs, and attach photos or documents. This ensures that inspection items can be evaluated clearly and logged correctly.
4. Desktop & Mobile-friendly Options
The best modern inspection applications include both desktop and mobile accessibility for both employees at the office and desk less staff alike. Solutions provide a seamless, user-friendly mobile experience so your team can easily work through inspections on the go and automatically share and log inspection data. Leadership can easily view details and further information from the desktop application anytime.
5. Comprehensive Reporting
Finally, a solid digital inspection solution will include comprehensive and customizable reporting features that allow you to dig deep into inspection data. With a solution like Some Management, you’re able to compare inspection items to spot patterns quickly and better plan for the future. As a result, you’ll spend less time putting out fires and more time avoiding them altogether!
Inspection Management Overview
The design and production of a product are impacted by the degree of objectivity, force, and dependability of the inspection management process. By keeping an eye on the product’s quality as it progresses through the manufacturing process, you can ensure that it will live up to customer expectations. Quality Inspection Management (QIM) allows for the streamlining and management of the inspection process’s difficulties. Depending on the requirements of your process, you can perform inspections at the incoming, production, or pre-shipment levels. Use the pre-configured AQL table or pick your own sample size. You can efficiently: do this with the help of quality inspection management.
- Get the inspection started
- Give more details about the example inspection plan.
- to carry out ongoing, post-production, and pre-production inspections.
- Finding Nonconforming Materials and Producing an NC Report
- Check the Samples Again
- Create the sampling/AQL standards.
- lowering risks
- Validate electronic signatures.
Conduct inspections
You can prevent non-conforming materials from entering the production process or from leaving your warehouse by standardizing the inspection procedures. Creating ad hoc tasks that you want to complete before or after the inspection of materials to ensure quality and safety is simple with our user-friendly system.
You can schedule inspection approvals and ad hoc tasks using QIM to gain more control over the inspection. Wouldn’t you like to discover the best management practices for inspection processes for efficient quality control?
What benefits do businesses get from Hsin Quality Inspection Management?
By establishing adaptable Inspection programs with Hsin Quality, you can streamline Inspection procedures in your company to address issues with job quality and demonstrate to regulators that your quality policies are effective.
You can manage your inspections with Hsin Quality.
- Give examples of the sample plan and inspection standard
- Improve the efficiency of incoming, in-process, or exiting inspection
- Reduce Supplier Risks
Managing Quality Inspections for Every Industry Skillfully with Quality Inspection Management
Quality Inspection Management manages job-related Inspection programs while demonstrating compliance with relevant regulatory standards for all industries, including hospitality, manufacturing, life sciences, pharmaceuticals, medical devices, cannabis/hemp/CBD, nutraceuticals, biologics, biotech, food and beverage, automotive, aerospace, defense, and logistics.
Among the features of the Quality Inspection Management Solution:
- Regional Database
- Criteria for Pre-Defined Inspections
- AQL Reporting and Dashboards-Based Sample Plans
- Email Approval Robot
- Reminders and Alerts
- E-Signature
- Unbroken Integration
- additional chatter